API 600 Gate Valve
1. Product Overview
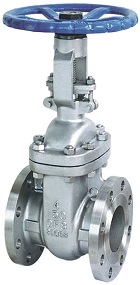
A cast steel API 600 gate valve, bolted bonnet, OS&Y, SS304, RF flanged ends.
The API 600 gate valve supplied by Metals Valve is a typical wedge gate valve which uses two inclined seats and a slightly mismatched inclined gate that allows for tight shutoff, even against higher pressures. The inclined seats are designed 5° to 10° from the vertical plane, while the inclined gate can be designed with a close, but not exact angle. When the seat and gate angles are slightly mismatched, either the seat or gate is designed with some free movement to allow the seating surfaces to conform with each other as the hand-wheel or actuator force is applied. API 600 is the standard specification for steel gate valves with flanged or butt-welding ends and bolted bonnet which are designed for heavy duty applications such as petroleum refinery and related applications where corrosion, erosion and other severe service conditions would indicate a need for full port openings, heavy wall sections and large stem diameters.
Design & Manufacture Standards: API 600, API 6D, ASME B16.34, ISO 10434, ISO 14313; Pressure Test: API 598; End Connections: RF/ RTJ-ASME B16.5/ ASME B16.47 Series A & B, BW-ASME B16.25; Face to Face Dimensions: ASME B16.10. Serial Number: APGV18. See the drawing and dimension-weight specification of APGV18.
2. Design Features
Operation
Hand-Wheel | Pneumatic | Electric |
![]() | ![]() | ![]() |
End Connection
RF | RTJ | FF | BW |
![]() | ![]() | ![]() | ![]() |
Bolted Bonnet
150LB | 300LB | 600LB | 900LB |
![]() | ![]() | ![]() | ![]() |
Pressure Seal
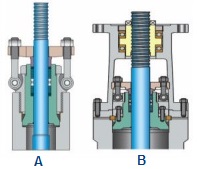
The pressure sealed bonnet design for 1500LB and 2500LB API 600 gate valves.
The pressure-sealed bonnet overcomes the weight disadvantages by letting the fluid pressure tighten the bonnet joint. The bonnet seal therefore becomes tighter as fluid pressure increases. This construction is frequently preferred for Class 1500 & Class 2500 API 600 gate valves that are operated at high pressures and elevated temperatures.
Other Features
(1) Wedge(disc): one-piece flexible wedge or solid wedge. Integral rib face design assures self-aligning of the wedge.
(2) Double-Stem Packing to assure low emission and tight stem sealing.
(3) A Lantern Ring is furnished at back seating for sealant injection or leakage-collection & drain.
(4) Bypass design to relieve the seating load prior to opening the valve at high pressure applications.
(5) OS&Y(Outside Screw & Yoke): the screw for raising or lowering the stem is located outside the valve body(rising stem).
(6) Live Load Packing: Belleville springs are employed to provide constant packing gland stress.
(7) Hard Faced Seating to assure durable wear resistance of the seating surface.
3. Material Selection
Technical Drawing

The technical drawing of conventional API 600 gate valves.
Zoom-In A | Zoom-In B |
![]() | ![]() |
Materials Selection
Item | Part Name | Material |
---|---|---|
1 | Grease Injector | SS304 |
2 | Yoke | A216 WCB; A217 WC1, WC6, WC9, WC11, C5, C12; A351 CF8, CF8M, CF3, CF3M |
3 | Yoke Bolt | ASTM A193 B7, B16, B7M, B8, B8M; ASTM A320 L7 |
4 | Hand Wheel Nut | ASTM A194 8 |
5 | Hand Wheel | Ductile Iron or Carbon Steel |
6 | Stem Nut | Copper Alloy, ASTM A439 D2 |
7 | Stem | ASTM A182 F6, F304(L), F316(L), F321, Alloy 20, 4140, 4340, 17-4PH |
8 | Gland Flange | ASTM A216 WCB; ASTM A351 CF8 |
9 | Packing Gland | ASTM A276 T410, T304(L), T316(L), T321, Alloy 20 |
10 | Packing Bolts | ASTM A193 B7, B16, B7M, B8, B8M; ASTM A320 L7 |
11 | Packing | Graphite or Braided Graphite |
12 | Packing Spacer | SS316/ SS304 |
13 | Backseat Bushing | ASTM A276 T410, T304(L), T316(L), T321, Alloy 20 |
14 | Bonnet | A216 WCB; A217 WC1, WC6, WC9, WC11, C5, C12; A351 CF8, CF8M, CF3, CF3M |
15 | Bonnet Gasket | SS316+Graphite, 1038, SS304, F304L, F316L |
16 | Bonnet Bolt | ASTM A193 B7, B16, B7M, B8, B8M; ASTM A320 L7 |
17 | Body | A216 WCB; A217 WC1, WC6, WC9, WC11, C5, C12; A351 CF8, CF8M, CF3, CF3M |
18 | Gate/Disc | A216 WCB; A217 WC1, WC6, WC9, WC11, C5, C12; A351 CF8, CF8M, CF3, CF3M |
19 | Seat Ring | ASTM A182 F6, F304(L), F316(L), F321, Alloy 20 |
20 | Lantern Ring | ASTM A276 T410, T304(L), T316(L), T321, Alloy 20 |
21 | Plug | SS304 |